Non-Compliance of HACCP and how IoT can help
Hazard Analysis Critical Control Point (HACCP) is a systematic approach to food safety that aims to prevent contamination and ensure food products are safe for consumption.
HACCP standards remains a significant issue in the food industry, leading to foodborne illnesses, product recalls, and financial losses. The Internet of Things (IoT) offers a transformative solution to these challenges by providing real-time monitoring, automation, and enhanced traceability. This article explores the non-compliance issues of HACCP and how IoT can significantly improve compliance through day to day practical examples.
- Manual Monitoring and Record-Keeping- These are two examples of traditional data monitoring and recording techniques that can be laborious and prone to human mistake. This may result in insufficient or erroneous documentation, which makes it challenging to prove compliance in audits.
- Lack of Real-Time Data- In the absence of real-time monitoring, critical control point (CCP) deviations could go undetected until it’s too late, which could lead to the production of contaminated food products.
- Inefficient Traceability- Manual processes may make it difficult to identify the source of contamination in the case of a food safety problem. Significant financial losses and broad recalls may result from this lack of traceability.
- Resource Constraints- SMEs may find it difficult to obtain the resources needed to establish and uphold strict HACCP protocols.
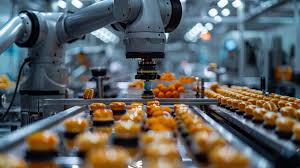
How IoT Helps in The Compliance Of HACCP Regulations
Real-time Monitoring and Alerts
Critical parameters including temperature, humidity, and pH levels are continuously monitored by IoT sensors. This real-time data makes it possible to identify deviations from established criteria right away and take swift corrective action. For instance, if a refrigeration unit’s temperature falls below the acceptable limit, the appropriate staff can be notified so they can act right once.
Enhanced Traceability
From raw materials to completed goods, IoT devices can follow products all the way through the supply chain. In the event of a food safety incident, this end-to-end traceability facilitates prompt identification of the contamination source, allowing for a quicker and more efficient resolution.
Automated Compliance and Reporting
IoT technologies eliminate the need for manual inspections and logging by automating data collecting and reporting. This ensures precise record-keeping while reducing human error and saving time. During audits, it is simple to generate automated reports that show compliance.
Cost Saving and Improved Productivity
IoT can result in substantial cost savings by cutting waste, lowering the possibility of product recalls, and improving resource use. Profitability and expansion can also be fueled by increased efficiency and productivity from less physical work.
Predictive Insights for Proactive Compliance
IoT systems that use predictive analytics can examine both historical and current data to spot possible risks before they become more serious. By taking a proactive stance, problems are avoided, compliance is strengthened, and interruptions that can erode customer confidence are avoided.
Remote Monitoring and Control
Food safety managers can supervise procedures from any location because to the Internet of Things’ ability to remotely monitor and control crucial control points. This adaptability permits real-time modifications and guarantees ongoing compliance.